This is a huge question; what is in a surfboard? There are many ways to make surfboards and the evolution of surfboard materials is complex. I will do my best, with the experience that I have.
I will start with the two types of foams commonly used for making surfboards; Polyurethane and Polystyrene. In California during the 1950s modern surfing developed around these two foams.
Polyurethane (PU)
PU has been at the core of surfboards since 1958. When you see a photo of a surfboard, it was almost certainly made from PU. This foam is simple to fibreglass, with easily sourced polyester resin. It has served well, as the basis for the surfboard industry for fifty years. PU blanks are made from a complicated mixture of chemicals poured into a concrete mould. The liquid foam expands and hardens and is then removed from the mould. The blank is cut lengthwise and a wood stringer is glued in giving the blank some rigidity.
Polystyrene
There are two variants of Polystyrene; Expanded Polystyrene (EPS) and Extruded Polystyrene (XPS)
EPS is made of little beads of foam which are put into moulds, then heated and fused together. This is mostly seen in packing, for example around new electronic goods. You can pull the beads apart with your fingernail. The foam can be very light where the beads are large and the foam is soft, or with more compression the beads are smaller and more dense and the foam is heavier. XPS (which looks similar to PU) is made of closed-cell bubbles blown in a liquid which hardens in a mould. XPS has been less popular in surfboards than EPS.

Foam and Resin
The biggest difference between the foams is how they react to polyester resin. PU foam works well with polyester resin while EPS and XPS melt when the come in contact with polyester resin. In the 1950s polyester resin was cheap and abundant and this led to the creation of millions of modern surfboards made from PU blanks. The other type of resin is epoxy resin which works well with EPS and XPS foams. Glassing with epoxy resins is common now, but in the 1950s to the 1990s epoxy was cumbersome to use and far more expensive than polyester resin.
Bob Simmons
Although PU blanks became the surfboard standard starting in 1958, EPS was used by Bob Simmons, one of California’s top surfboard artisans from around 1950-1954. At that time, surfboards were either wood or Bob's EPS and plywood sandwich method. Bob was searching for a lighter, faster surfboard. He shaped the EPS and then glued plywood to the top and bottom and then added balsa rails. These boards were very light, extremely fast and easier to make than the wood boards. Simmon’s methods may have become the dominant paradigm for surfboard manufacture and surf history may have been very different with his designs, however Bob Simmons died surfing Wind’n’Sea in California in 1954. Simmons’ surfboards were essentially forgotten for nearly 40 years.
RIP Clark Foam
By 1958 Hobie Alter of Hobie Surfboards, working with Gordon Clark, created a chemical mix for making Polyurethane (PU) blanks. Clark was a pioneer in the ‘dark art’ of making surfboard blanks. The chemical mixtures needed to make the blanks are complex and the process is highly toxic. It took several years to master. The chemical recipes for the blanks were secretive and closely guarded.
While Clark was inventing the PU surfboard blank, the popularity of surfing was beginning to explode. Gidget, the story of a young surfer girl at Malibu in 1957, was on the bestseller list and the Gidget movie was a box office hit. Surf music was becoming tops of the charts. Even Elvis was surfing in the 1960 movie Blue Hawaii. Surfing had moved from a fringe culture to enormous popularity. You can read more about modern surfing history here
Clark Foam surfed this wave of popularity and was the USA’s top supplier of surfboard blanks. Australia made their own PU blanks. Just as Clark had guarded his secrets for manufacturing blanks, he guarded his near monopoly on USA blanks. His tactics for suppressing competitors are legendary and were very successful. (Later, I was a part of the resistance against Clark Foam. I was experimenting with EPS foam and worked as a sales rep for the competitor, Walker Foam). Suddenly, on December 5th 2005, Clark shut down his factory and destroyed the cement surfboard blank moulds. This was known as ‘Black Monday’ and many surfboard manufacturers panicked. Overnight their supplier had vanished. Some rejoiced, like myself, who finally felt that surfboard blanks would be made to a much higher standard and environmentally sustainable.
During the Clark Foam era from 1958 to 2005, EPS foam had not altogether disappeared from small, backyard manufacturing. In 1985 I was approached by a guy who had the most epic backyard surfboard factory I have ever seen. He had made a mould for an EPS 7’ egg and I loved the way the board surfed! He had an excellent glasser finishing and glassing the boards, who lived in his backyard.
At that time there was a big issue with glassing EPS with polyester resin. Polyester resin was the standard for glassing but it would melt EPS if it came in contact with it. The answer was sealing the EPS shapes with common, water-based wood glue. The glue would create a barrier between the EPS and the polyester resin. This sounds ridiculous now, but was standard in California back then. Nearly 40 years later I told this story to Bob McTavish. He told me he had used normal house paint instead of glue. He had gone through the same process. Bob and many other surfboard shapers loved the feel of EPS when surfing.
1990s Experimentation
Founded in 1989, Surftech began using an EPS core to construct their surfboards. They created a complex manufacturing method by taking a very light EPS core, wrapped with a dense foam on the outside and then glassed with an improved epoxy resin. The boards were made in mass quantities in Thailand and shipped around the world and this process is still used today. Despite being cheaper and more durable than PU boards, this EPS method has not displaced PU boards. Top surfers seldom surfed these boards. The issue was the feel was not quite right. Surfboards have a feel which experienced surfers come to understand, yet can seldom explain in detail. I will attempt to talk about the feel now.
The Feel of Different Surfboard Materials; PU, EPS, XPS and Balsa
It’s all in the vibe, man! This is a difficult topic to write about because words are clumsy when attempting to share a sensation, especially the complex sensation of surfing. I will attempt to explain the different sensations of the foams and woods through my own experiences. As a young Southern Californian surfer, I had the unique opportunity to feel and see the surfboards from the past and understand the evolution of surfboard materials and design.
In the 1970s I was surrounded by the shortboard revolution and surfboard shapes changed dramatically from year to year. Each summer, surf movies came to the legendary Cove Theatre in Hermosa Beach and the whole surfing community would see the latest evolutions. Many kids made their own surfboards and the crew at ET Surfboards (since 1972) were very helpful with supplying all the surfboard blanks, resin and materials. I was making surfboards by 1979. It was a time when we were hugely self confident and believed we were changing the world through surfing.
Although I was swept up in the vibe of the 1970s, I was aware of different cultures which existed prior, the 1960s and even earlier. Endless Summer would regularly play on TV and I was familiar with that genre of surfing. At that time, 1960s longboards were abundant and not valued. My few longboarder friends and I bought them for cheap and considered ourselves rebels for embracing the old style. I owned many of these boards and I preferred the boards with thick wooden stringers. They were heavier, but I loved the feeling.
I became enamoured with the 1960s surf culture. It was only a decade or so before, but it seemed so far away during my informative high school years. The shortboard revolution was evolving at such speed, there were few reminders left of the Golden Age of Surfing, aside from numerous old boards sitting in garages and forgotten films. When I was around 10 years old (1975) my family would take our boat to the gas dock and Hap Jacobs manned the pump. He was very friendly and I remember his warm wide smile. My father told me he was once a great surfboard shaper. It seemed like he was shaping in another age, but in reality he had probably sold his Jacobs Surfboard shop just five years earlier. In the surfing world there was a huge change in culture from the 1960s to the 1970s.
In the late 1970s I regularly surfed the Palos Verdes Cove with ‘old David Constable’. He was a friendly gentleman who had spent his life surfing and he told me of living at Waikiki in the 1930s and surfing with Duke Kahanamoku. One day in 1978 David’s sons paddled out on his old wood Waikiki plank surfboards. I was astonished by the incredible speed of those boards. They caught the swell much further out and went across the wave much faster than I thought possible. Watching the boards on this day and talking with David of old times gave me a rare glimpse into the age of wood surfboards.
The Eighties
In 1983 I had the use of three balsa wood longboards and I loved the way they surfed. They were heavy on land but lively and buoyant in the water. I surfed an 11 foot Hobie Malibu Chip and it seemed to jump out of turns and felt natural on the wave. I would have loved to surf them all the time but the resin was old and brittle and they leaked, so the board quickly filled with water. Patching the old boards seemed too difficult and I was actually destroying the boards by surfing them. I had heard that Phil Edwards preferred balsa wood over foam and I understood why. Many years later Tom Curren told me a similar story and he stopped surfing balsa because patching dings was problematic, however balsa wood has its own unique feel that is fantastic.
In 1987 I surfed my first EPS surfboard as mentioned it above. On my first wave I was reminded of the feel of balsa. The board jumped out of turns more than a PU surfboard and I loved it, but it broke in half soon after.
I was so impressed that I tried to make my own EPS board with epoxy and failed. The epoxy resin was temperamental in the 1980s and my first lamination ended up draining off the board and onto the garage floor. Once I successfully glassed it, I dinged the board on the way to the surf and the board filled with water, which also leaked all over the garage floor. The EPS of that time was lower density and would absorb water like a sponge when sealed in fibreglass. At that time EPS was seemingly impossible to use for surfboards though it felt great in the water, for a short time.
A few years later I was a team rider for Donald Takayama. He was having a hard time with Clark Foam and had turned to Extruded Polystyrene (XPS) blanks. Within the industry, Donald was secretive about trying the XPS blanks and as a team rider I had a prototype which I loved. It was the ‘magic board.’ I broke it and when I tried to put it back together with polyester resin, I created a smelly, melted mess and destroyed the board completely. Even I did not know it was XPS. Donald was the only surfboard shaper I knew who faced down Clark Foam's bullying tactics. But that is a story for another time.
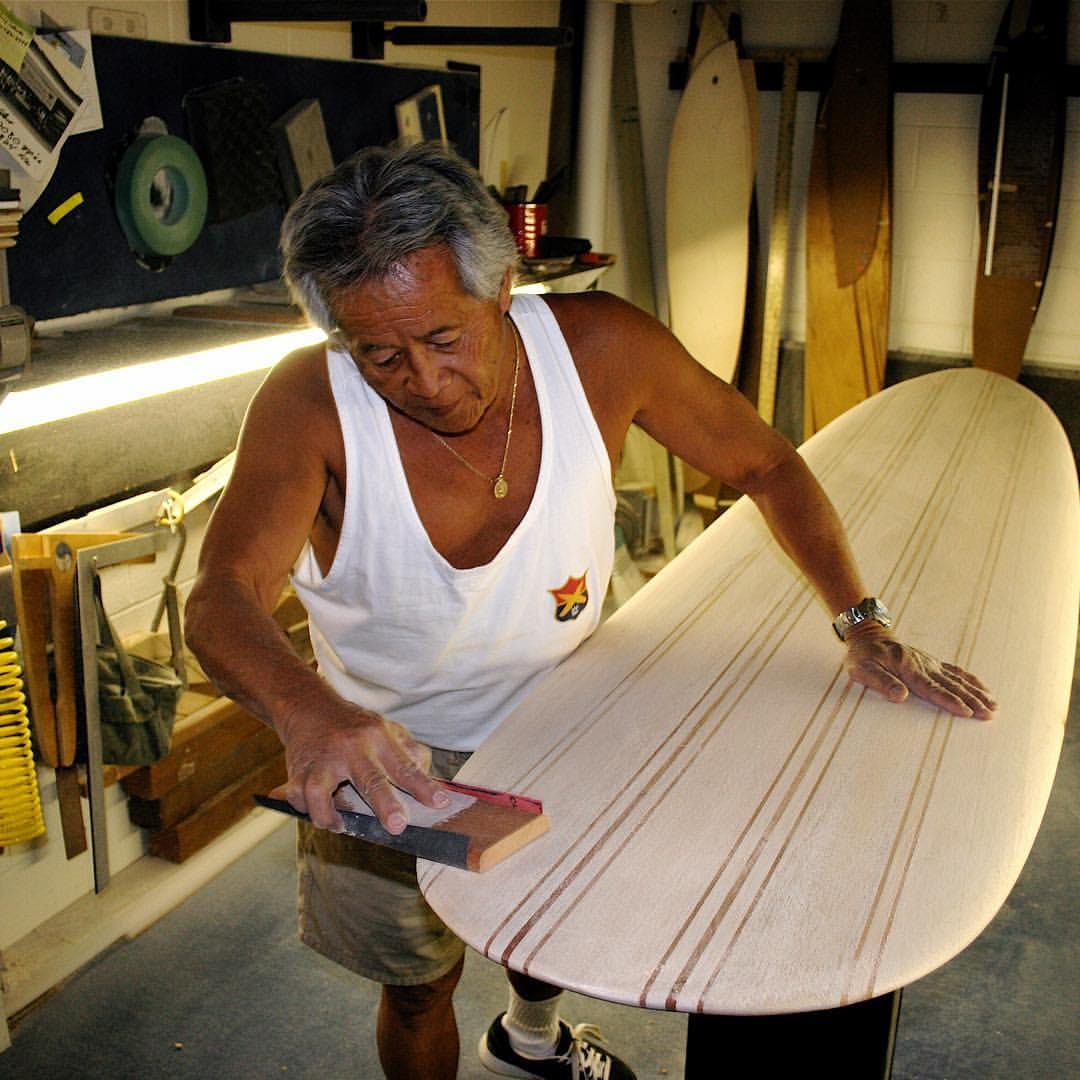
There is another benefit to polystyrene, EPS and XPS; you do not have to glass or seal it. In Australia in the 1960s and 1970s there were Coolite EPS boards that were made in a mould and not sealed at all. They were very popular. There were similar boards in the USA but I cannot remember their names.
The big anomaly with EPS is when it is not sealed, like the Coolite boards, it does not absorb water. However when it is sealed it does absorb water. In Australia this was seen with the unsealed coolite boards vs the lifesaver paddle boards, which were glassed and absorbed water quickly when dinged.
The differences between PU and EPS
PU must be sealed or glassed while EPS does not need to be sealed
PU does not have the bounce and memory of EPS
PU comes in surfboard blank form and the foam on the outside of the blank is structurally stronger than the foam in the middle of the blank - EPS blanks are cut from large blocks of foam and the density is consistent throughout the block
With PU blanks you need the right blank to make a specific board - you need a 12’ blank to make a 12’ surfboard - with EPS any size blank can be cut from a block to make any size of board
PU can be sealed with most common sealants while EPS melts with polyester resin, oil based varnishes and turpentine
I have focussed on EPS foam so far because it is little understood while the normal surfboard foam (PU) is well known and still used by the pros. I believe modern surfing has evolved around the PU blank and polyester resin. The pros get a steady flow of new boards and find they have a great feel, though after a few surfs, the bounce is not as good and they get a new board. PU blanks have evolved and they are lasting longer now, however the people who pursue a different feeling, like me, are on the fringe of surfing. If you are interested in this article, you are probably in the curious shaper/surfer camp who are ever-searching for a deeper surfing experience.
So many materials, so many perspectives; we can learn from them all
In 2010 I was experimenting with another concept of surfboard design which I called the Tunas, which were finless surfboards. I was chasing a very particular feeling on a wave - like my flexible wood alaia boards but with more floatation. I was using EPS and following Ryan Birch and Cyrus Sutton’s concept with the EPS Lord Board just making them longer and stronger so they would not break so often. I was evolving the shapes very fast. I would cut an EPS blank, glue some stringers, shape it and surf it with only a coat of water based varnish. I really enjoyed this process and through it I created The Seaglass Project with my wife, Margie. We licensed the Tuna and the Albacore boards to Global Surf Industries at the time.
While experimenting with these boards I found that sealed EPS will not absorb water if the density of the EPS is greater than 28kg. For me this was a big deal and this knowledge has influenced how I make my cork and wood boards now.
When I was at the 2011 CARV Expo, a surf and skate trade show in San Diego promoting The Seaglass Project boards with Global Surf Industries, Donald Brink shared a mind expanding design innovation with me. He told me how he shapes EPS boards and then glasses them with common fabric and water based varnish. This has influenced the way I make surfboards now and opened the door to any surfboard maker in the world. These three ingredients can be found just about anywhere and one's own imagination is the only limit to new surfboard designs.
There is a world of foam outside the two I have mentioned. I do not discuss the boogie board foams or the soft board foams because they are very difficult to shape. The foam does not sand with sand paper and is not for shaping by hand. I have little experience with them and they seem to be outside the realm of the small, artisanal surfboard maker.
The essence to these stories is that there has been a tension between balsa wood, EPS and PU foam since 1958 when PU foam (polyurethane) was brought into the surfboard world by Gordon Clark. From my perspective Balsa was the best, EPS was second (but so difficult to glass) and PU was third. However for the surfboard industry PU was clearly the material of choice, then EPS (which was finally mastered by Surftech), while balsa continues to be difficult to source and maintain.
(Note: balsa has been used successfully for many years by Riley Balsa in Australia).
Once again, I must point out that my perspectives come from my own experiences and all opinions are my own.
Footnote: In the final editing stages of this article, Margie and I met Dan from Grow Blanks based in Kenya, Africa. The blanks are made from the wood of the agave stalk. They are biodegradable and eco-friendly, providing a totally viable organic option to surfboard foam. Dan and Tom pictured below with Grow Blanks.
"When I was at the 2011 CARV Expo, a surf and skate trade show in San Diego promoting The Seaglass Project boards with Global Surf Industries, Donald Brink shared a mind expanding design innovation with me. He told me how he shapes EPS boards and then glasses them with common fabric and water based varnish. This has influenced the way I make surfboards now and opened the door to any surfboard maker in the world. These three ingredients can be found just about anywhere and one's own imagination is the only limit to new surfboard designs."
I'd like to hear more about this, Tom. Can't find anything online. Possibly a cheaper way for backyarders to test shapes before committing to more expensive laminates?
Stu, thank you very much for the comment. Happy that you are following! You are absolutely right. It is a great way to quickly and cheaply test your design ideas and that is exactly what I did. When we dive deeper in the 'how' to make surfboards I will be sharing more on this topic.